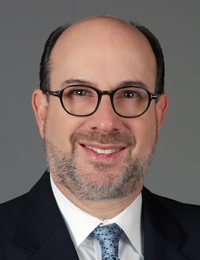
The regulations for container ships, in most cases, have little to do with the business of air cargo. But the fate of at least one vessel, the MOL Comfort, one of the largest container ships ever lost at sea, could have implications on air cargo handlers, especially this summer, when new rules will kick in requiring that stated container weights must be verified.
According to big-container-ship design standards, the MOL Comfort was built to withstand even the most punishing seas under the harshest weather conditions. But in June 2013, the 9,100-TEU-capacity ship, with only about 4,500 containers aboard, broke in two during a storm in the Arabian Sea while sailing from Singapore to Jeddah. Fortunately, the 26-member crew was rescued and brought to safety before the rest of the ship broke apart and sank while being towed to salvage.
After the loss of the Comfort, investigators began to examine similar past maritime accidents involving cargo ships, with a particular emphasis on the weights of the containers themselves. While most of the evidence from the Comfort vanished at sea, cargo boxes from the MSC Napoli, an earlier wreck that beached itself off the cost of England in 2007, were partially saved. Of the more than 600 dry containers recovered, 20 percent differed from the declared weight, for a total in excess of 312 tonnes more than what the manifest showed.
Despite accommodating large loads of cargo and fuel, modern container vessels are designed to flex while in transit to withstand harsh sea conditions. Still, each has inherent limitations that improperly balanced cargo – coupled with adverse wind and sea conditions – might exceed, causing structural failure and disaster.
The International Maritime Organization, or IMO, the United Nations’ special agency that develops and maintains a comprehensive regulatory framework for shipping across the world, is responding to false container weight declarations as the culprit for these and other past maritime mishaps. The entity has made amendments to its Safety of Life at Sea (SOLAS) regulations that will make it mandatory for containers to have their stated weight otherwise verified. This regulation is set to be in force at the beginning of July of this year.
Despite shipper and forwarder concerns about the requirement, experts continue to argue, but most agree that undeclared container weights may have played a role in past vessel disasters. But placing the blame solely on under-declared weights could be a costly mistake. As the world economic situation creates increased competition between vessel operators, port operators could be pressured to offload and reload ships faster than ever. Rushing creates an environment where load planning errors result in dangerously unbalanced placement of containers that could test a ship’s resistance to moving forces. In other words, the containers themselves may be only part of the problem.
Regardless of the reason, it’s fair to say that the requirement will stay and, despite only half of the shipping and forwarding community being in various states of readiness, July will be here before we know it.
Two weighing methods will be acceptable, including using a scale to weigh the container, subtracting the truck, driver, chassis and fuel, or adding the weighed contents to the tare weight of the container. Unanswered questions remain about how the mandate affects them, what the responsibilities are for each party, the definition of the required certification and who will complete the overall task of reporting the verified gross mass of containers to the vessel operator.
Not addressing these important questions while imposing the rule under unclear circumstances could create time-consuming port delays as shipper and trucker uncertainty over the new regulation causes congestion. As we saw last year, during the U.S. West Coast port labor slowdown, such interruptions can have profound adverse implications for all ports and the overall economy.
Air cargo interests, responding to this lack of clarity, are beginning to see the uncertainty as an opportunity, similar to the harbor congestion that created more than 200 ad hoc air charters and full airline plane bellies of cargo last year. This could be wishful thinking, perhaps, as the surge came from backlogs of import and export containers, both in and out of U.S. ports. Some experts say that such container-weight-related congestion may not occur outside of Asia, where export activity is most prevalent, due to trade imbalances.
As forwarders, we should take a page from the recent air cargo screening mandate by encouraging a balanced, multitiered approach to addressing the requirement. We should work with the maritime shipping community in combining resources to get the container weights verified.
For instance, terminal operators could provide weighing services, both at and away from the port, as an alternative. Drayage firms could join forces with independent companies, offering weighing services to meet the mandate before the container arrives at the dock. Or forwarders and non-vessel operating common carrier (NVOCCs) could invest in pallet weighing equipment to verify shipper weights before container loading. Clearly, there are many other innovative solutions that can be applied to address the issue.
Forwarders are used to meeting the challenge of shifting markets and requirements to meet our customers’ changing supply chain needs. It may also be an opportunity to prove our resourcefulness and added value to them as well.